1. Optimisation of Supply Chain Layout and Enhancement of Risk Resistance
1. Establishing a “Dual-Track Supply Chain”
Diversify raw material procurement sources (such as importing petrochemical materials from Southeast Asia and the Middle East) to reduce reliance on a single market. For example, the Fulling Company is building a new factory in Indonesia to reduce high tariff barriers. At the same time, align with recycled plastic technologies (such as bio-based pets and water-soluble films) to reduce dependence on petrochemical materials, with the global tendency to reduce plastic use.
2. Adjustment of Regional Production Capacity and Logistics Optimisation
Set up production bases in low-tariff countries (such as Mexico and Vietnam) to shorten transportation cycles and reduce tariff costs. For instance, enterprises in South China have reduced hidden logistics costs by 20% by establishing factories in Southeast Asia. Additionally, optimise inventory management by introducing intelligent systems to monitor inventory turnover rates in real-time, thereby reducing storage costs.
3. Supply Chain Finance and Cost Hedging
Use futures hedging to lock in raw material price volatility risks, with leading enterprises adjusting customer pricing within a month when costs rise by 5% through a price linkage mechanism. Supply chain finance platforms can alleviate funding pressures for small and medium-sized enterprises, such as enhancing supply chain transparency through blockchain technology.
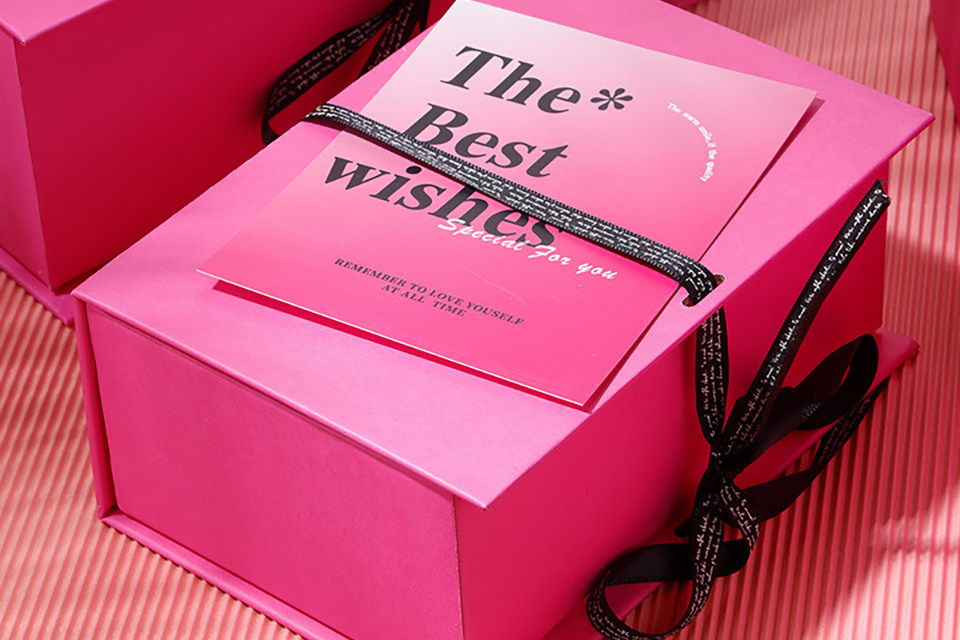
2. Diversification of Market Expansion and Exploration of Domestic Demand
1. Emerging Market Development
Increase exports in areas such as ASEAN and Africa with the amount of trade between China and ASEAN, is estimated to increase by 7.7% in 2024, indicating the regional market capacity. For example, paper companies are turning to the import of pulp and paper from Canada and Russia to change sources from the United States.
2. In-depth Development of Domestic Segments
Focus on high value-added sectors such as food and pharmaceuticals to develop customised packaging solutions, such as functional barrier films and intelligent temperature-controlled packaging. The domestic market can achieve growth through e-commerce packaging (expected to account for 52% by 2030) and cold chain transport packaging (with an annual growth rate of 18%).
3. Brand Upgrading and Service Differentiation
Establish brand barriers through environmental certifications (such as recyclable labels) and rapid response supply chains to avoid low-end price wars. For instance, Coca-Cola is exploring PET bottles as a substitute for aluminium cans to reduce tariff costs, despite facing challenges with recycling rates.
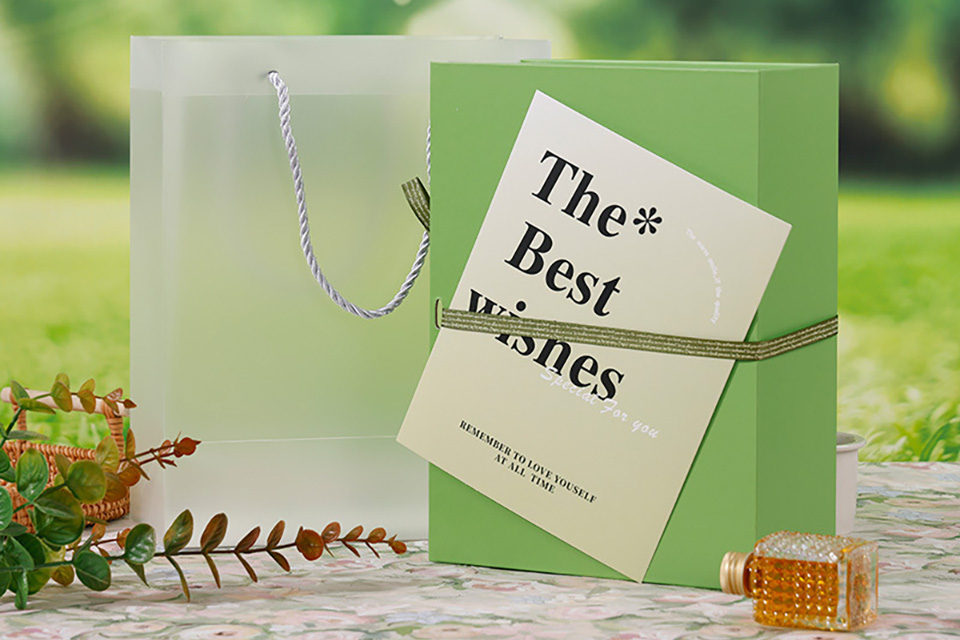
3. Technological Innovation and Product Structure Upgrading
1. Material and Process Innovation
Develop lightweight materials (such as ultra-thin aluminium alloys and coated iron) to reduce unit costs by 8%-10%. Promote UV-LED green printing technology to reduce solvent emissions and enhance production efficiency by 30%.
2. Intelligent and Digital Transformation
Introduce AI scheduling systems and digital twin technology to improve inventory turnover rates by 25%, with leading enterprises reducing labour costs by 40% through smart manufacturing equipment. For example, the metal packaging industry is adopting intelligent robots to achieve dark factory operations.
3. Application of Environmental Technologies
Develop biodegradable PLA films and bio-based materials to respond to the plastic reduction goals of the Paris Agreement. The EU carbon border tax is compelling enterprises to adopt circular economy models, with the coverage rate of plastic pallet recycling systems reaching 31%.
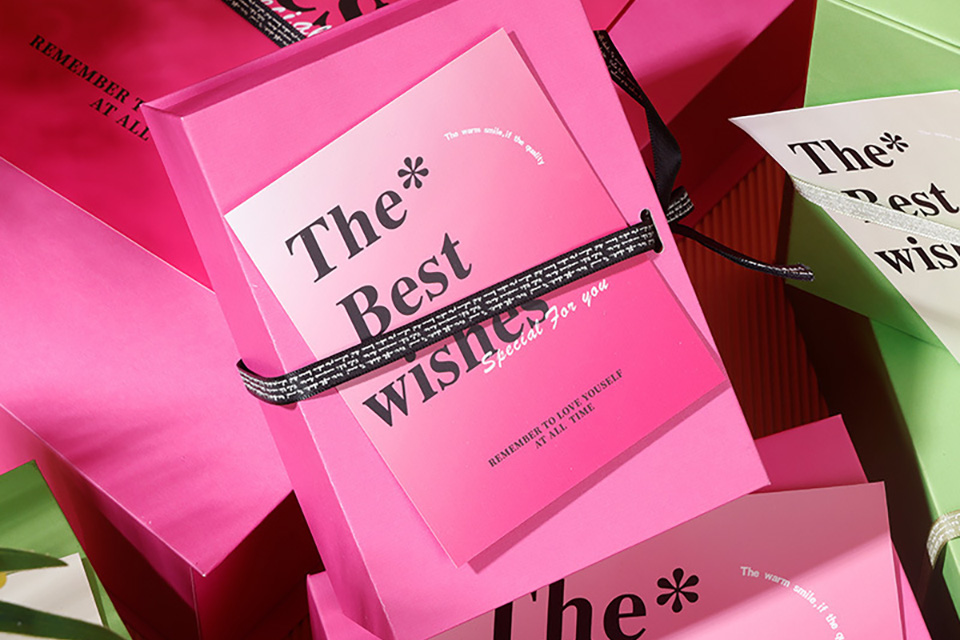
4. Industry Collaboration and Policy Leverage
1. Mergers, Restructuring, and Increased Concentration
Reduce inefficient capacity through consolidation, such as China National Building Material increasing the cement industry concentration from 12% to 70%. Leading enterprises are accelerating mergers and acquisitions of small manufacturers to form regional industrial clusters.
2. Utilising Policy Support
Apply for special subsidies for new materials and green manufacturing, such as the Ministry of Industry and Information Technology requiring an 18% reduction in energy consumption for transport packaging, promoting the transformation of heat pump drying technology. Participate in carbon trading systems to enhance ESG competitiveness through carbon footprint certification.
3. Collaboration with Industry Associations
Establish joint procurement platforms to lower raw material costs, such as paper companies reducing procurement prices by 5%-8% through bulk purchasing of waste paper. Promote the formulation of industry standards to enhance international influence.
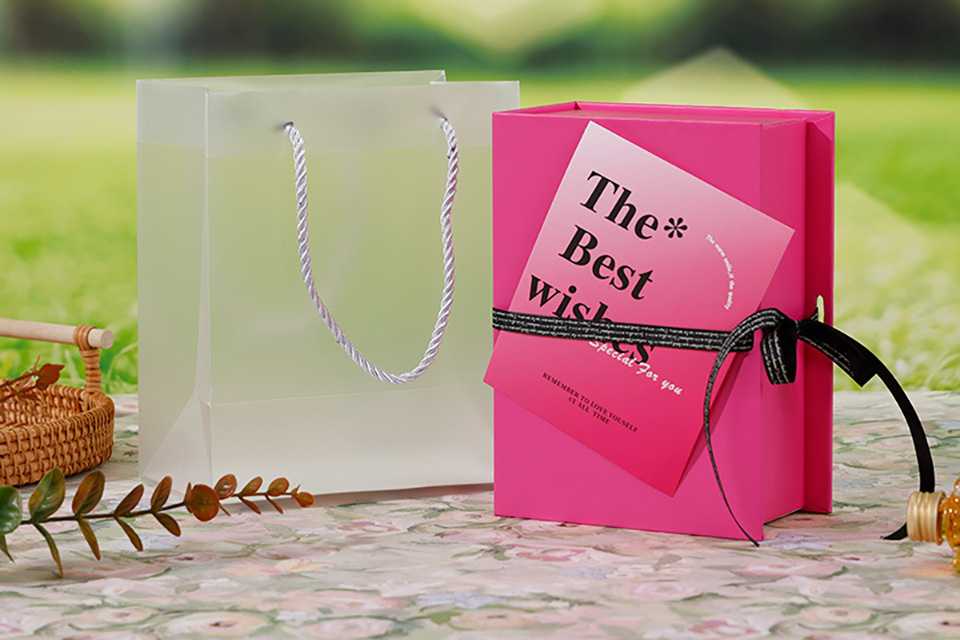
5. Risk Prevention and Long-term Strategy
1. Dynamic Risk Assessment
Establish a tariff fluctuation early warning model, utilising big data to forecast raw material price trends, and develop flexible procurement plans. For example, leading companies adjust their supply chain layouts three months in advance through AI analysis.
2. Emergency Response Mechanism
In response to the risk of supply chain disruptions, diversify supplier reserves to ensure the security of critical material supplies. For instance, paper companies establish their own forests to guarantee timber supply.
3. Sustainable Development Layout
Balance environmental investment with commercial viability, such as using solar power to reduce energy costs by 20%, while also applying for green credit support. In the long term, it is necessary to construct a technological pathway of “material lightweighting – structural modularisation – functional intelligence”.
Conclusion
The packaging industry needs to focus on “supply chain resilience + technological innovation + market diversification”, combining short-term cost control (such as regional capacity transfer) with long-term competitiveness building (such as green material research and development). At the policy level, it is essential to leverage industry integration and environmental subsidies, while at the enterprise level, enhancing risk resistance through digitalisation and collaborative cooperation is crucial. In the future, companies with vertical integration capabilities and low-carbon technologies will hold an advantage in the tariff wars.